Revolutionizing Interior Door Manufacturing: Top 2025 Tech Advances and How to Leverage Them
As we move closer to 2025, the interior door manufacturing industry is on the brink of a technological revolution that promises to redefine efficiency, customization, and sustainability. According to a recent report by the Freedonia Group, the demand for interior doors is expected to grow at an annual rate of 4.6%, driven by a resurgence in residential construction and home renovation projects, as well as a rising trend towards personalized living spaces. This shift highlights the urgent need for manufacturers to adopt cutting-edge technologies, particularly Interior Door Machines, that streamline production processes and enhance product quality.
In this rapidly evolving market, leveraging advanced machinery can significantly improve the competitive edge for manufacturers. A study from IBISWorld indicates that companies investing in automation and sophisticated manufacturing techniques see a potential increase in productivity by up to 30%. By embracing innovations such as computer numerical control (CNC) machines, artificial intelligence, and smart manufacturing processes, interior door manufacturers can not only meet the growing consumer demands for customization and efficiency but also contribute to sustainability goals by reducing waste and energy consumption. As we delve into the top technological advances expected by 2025, it's crucial for industry players to understand how to effectively integrate these developments into their operations.
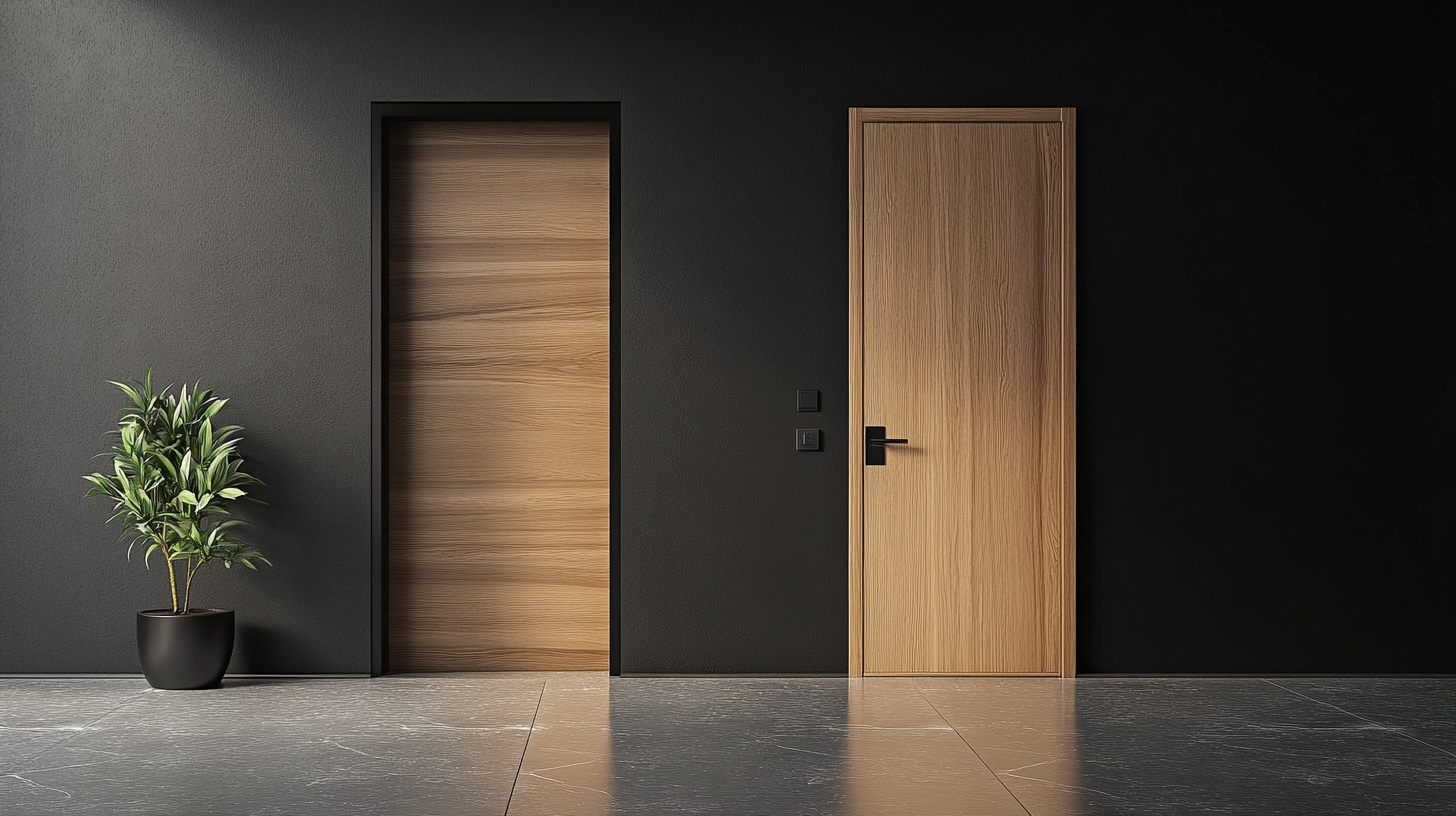
Emerging Technologies Shaping the Future of Interior Door Production
The landscape of interior door manufacturing is undergoing a remarkable transformation, driven by a myriad of emerging technologies. As we approach 2025, industry reports indicate that the global market for interior doors is projected to reach $39 billion, growing at a CAGR of 5.3%. This growth is largely fueled by advancements in automation and smart manufacturing processes, making production more efficient and cost-effective. One of the most compelling innovations is the integration of IoT (Internet of Things) in manufacturing. By 2025, it's estimated that nearly 50% of all manufacturing units will be equipped with connected devices that enable real-time monitoring and predictive maintenance. This technology not only reduces downtime but also enhances quality control throughout the production process. For example, sensors can detect anomalies in door production, allowing manufacturers to address issues before they lead to significant defects or delays. Moreover, the application of advanced materials and sustainable practices is shaping the future of interior door production. Reports indicate that the use of eco-friendly materials is projected to increase by 30% in the next two years, driven by consumer demand for sustainable living solutions. Manufacturers adopting these practices can not only appeal to environmentally conscious consumers but also comply with increasingly stringent regulations regarding carbon emissions. Lastly, integrating 3D printing into door manufacturing processes presents a unique opportunity for customization and reduced waste. According to a 2023 industry survey, over 40% of manufacturers are exploring 3D printing for creating customized designs that meet specific client needs while cutting down on material excess. This technology represents a significant shift towards more personalized production, ultimately enhancing customer satisfaction and operational efficiency.
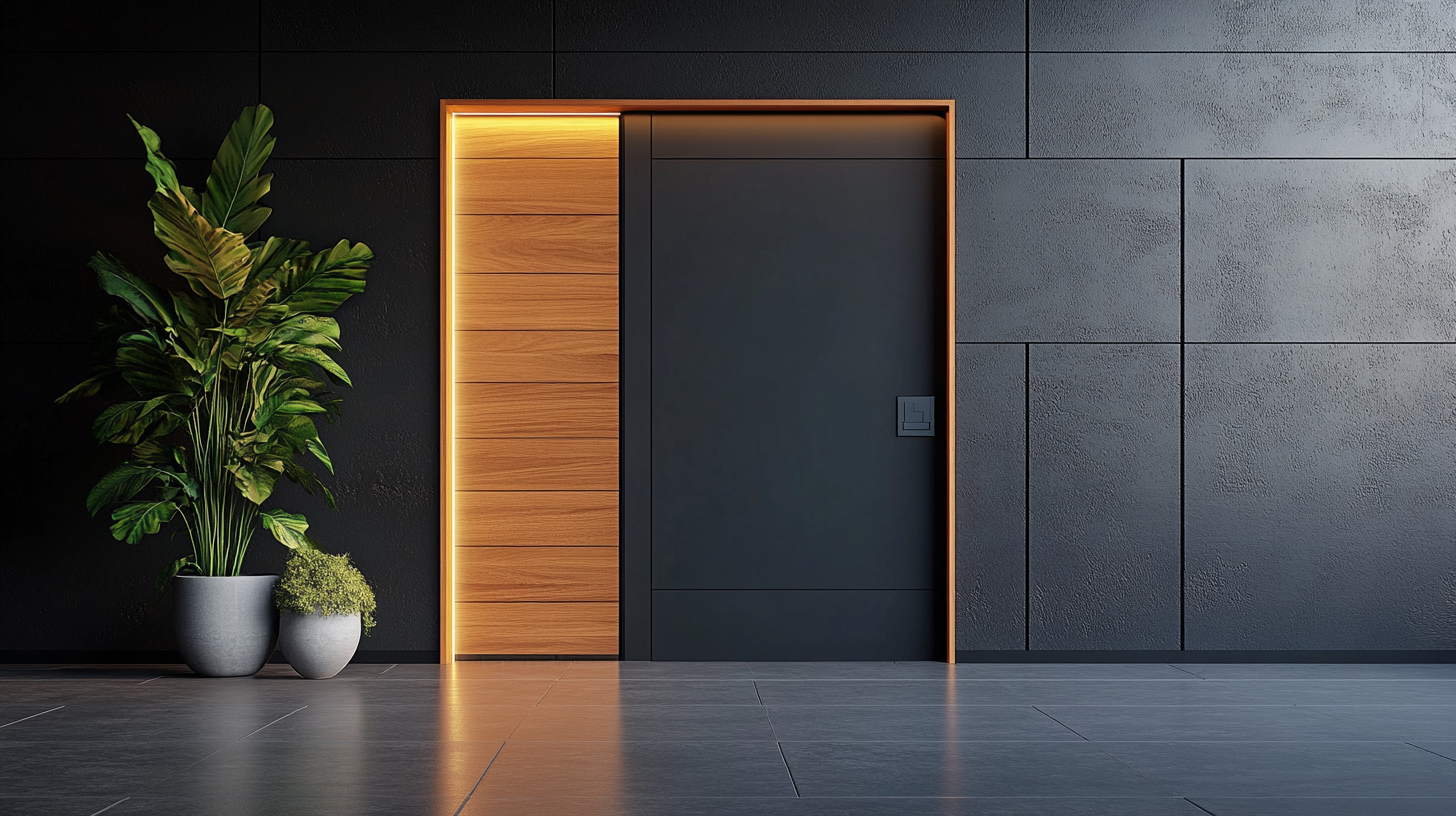
Smart Manufacturing Techniques: Enhancing Efficiency and Quality
The world of interior door manufacturing is on the cusp of a technological renaissance. As we move closer to 2025, the adoption of smart manufacturing techniques is proving to be a game-changer for enhancing both efficiency and quality in production processes. By integrating automation, IoT (Internet of Things), and advanced data analytics, manufacturers can streamline operations and reduce waste significantly.
One of the key advancements in smart manufacturing is the use of real-time monitoring systems. These systems allow manufacturers to track every stage of the production process, from raw material sourcing to the final inspection of finished doors. With sensors placed throughout the manufacturing floor, data is collected continuously, enabling manufacturers to identify bottlenecks, predict equipment failures, and implement preventative maintenance strategies. This proactive approach not only minimizes downtime but also ensures a more consistent and high-quality product.
Moreover, leveraging machine learning algorithms can greatly enhance the decision-making process in interior door manufacturing. By analyzing historical data and production metrics, these algorithms can forecast demand, optimize inventory levels, and tailor production schedules accordingly. This level of intelligence leads to more responsive manufacturing practices that can adapt to changes in consumer preferences and market trends, ultimately improving overall operational efficiency and quality assurance in the production of interior doors.
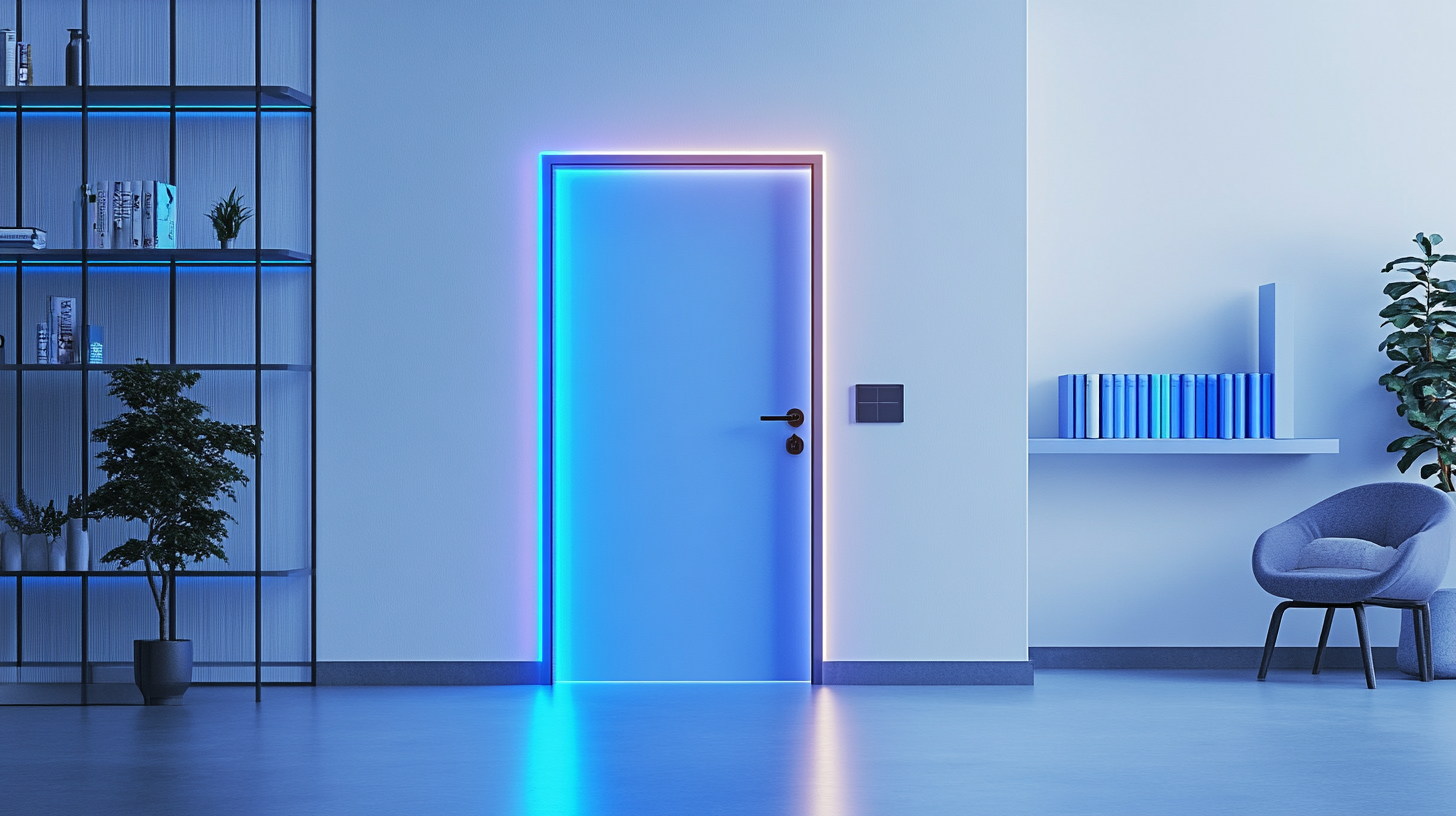
Sustainable Materials in Door Manufacturing: Innovations and Benefits
The focus on sustainable materials in door manufacturing is becoming increasingly crucial as industries strive to reduce their environmental impact. With innovative alternatives becoming available, manufacturers are exploring eco-friendly materials that not only enhance the performance of interior doors but also contribute positively to sustainability efforts. One notable development is the utilization of bioplastics derived from renewable resources, such as Azolla. This aquatic fern, previously overlooked, holds great potential as a sustainable feedstock that can significantly minimize plastic waste in the door manufacturing process.
Furthermore, the integration of recycled materials into door production is gaining traction. Many companies are now incorporating post-consumer recyclables and other sustainable substances into their products, reflecting a broader industry trend toward responsible sourcing. This approach not only conserves resources but also reduces the carbon footprint associated with the manufacturing process, aligning with global sustainability goals. By leveraging these advancements, manufacturers can create durable and aesthetically pleasing doors that meet consumer demand while protecting the environment.
Additionally, innovations such as spider silk-derived materials are emerging in the realm of sustainability. Known for its strength and durability, spider silk is being utilized in various applications, including door manufacturing, to design products that last longer and require less frequent replacement. Such innovations signify a shift in how manufacturers view materials and their impact on the planet. As the industry continues to evolve, embracing sustainable practices and materials will be vital for fostering a greener future in interior door manufacturing.
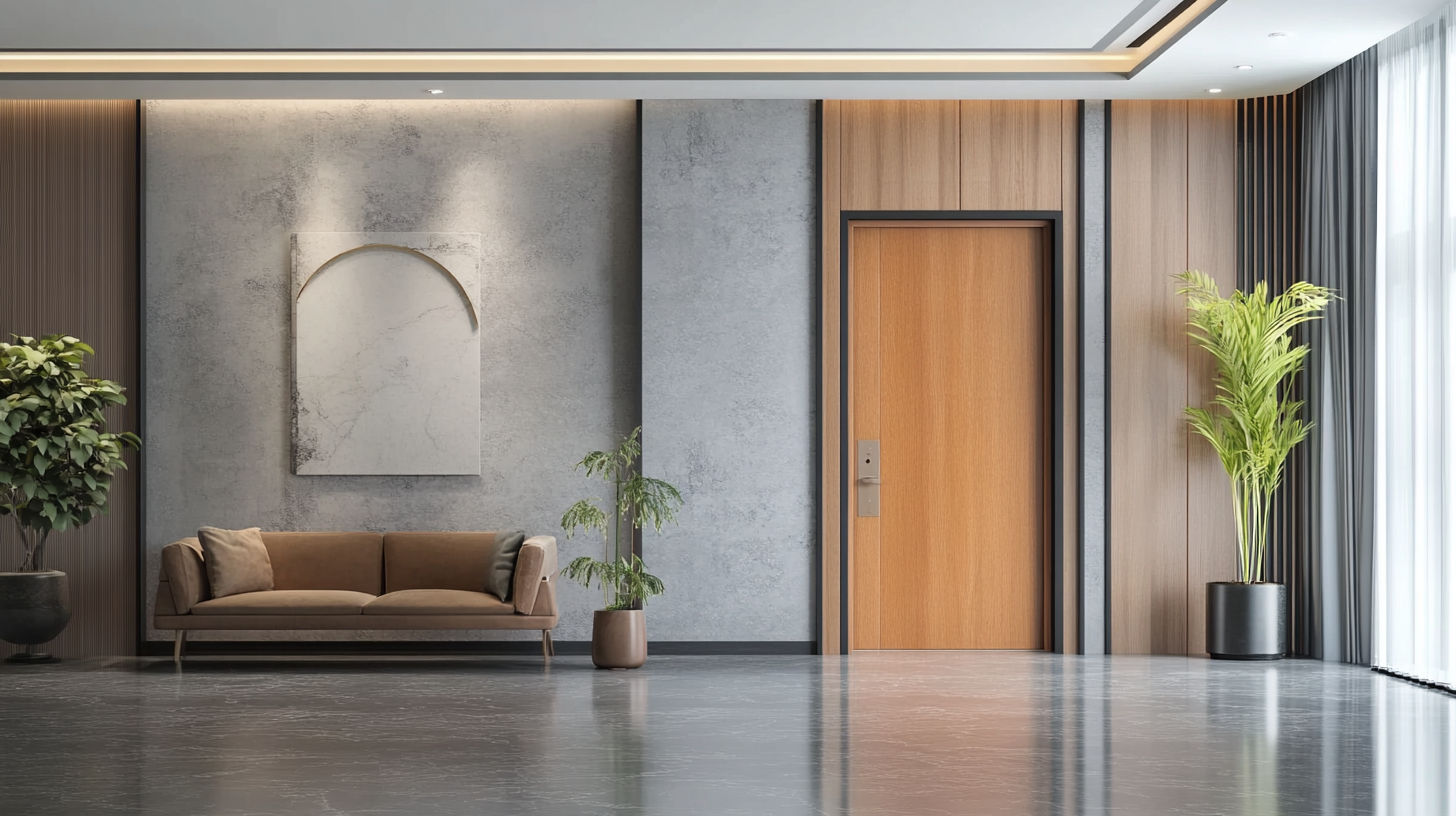
The Role of Automation in Streamlining Interior Door Design Processes
The advancement of automation technology is transforming the way interior doors are designed and manufactured, leading to unprecedented efficiencies in the industry. By integrating automated systems into the design process, manufacturers can streamline workflows, reduce human error, and increase production capacity. With the capability to execute complex design specifications with precision, automation not only enhances accuracy but also allows for rapid iterations, enabling designers to explore more innovative concepts without the usual time constraints.
Moreover, automation enhances collaboration within teams by enabling real-time updates and feedback throughout the design process. Cloud-based design software, combined with automated tools, ensures that all stakeholders can access and review designs simultaneously, fostering a collaborative environment that inspires creativity. This synergy between design and technology accelerates the overall development cycle, ensuring that new trends and consumer preferences are swiftly captured and implemented in new product lines.
As manufacturers look toward 2025, embracing automation tools becomes essential for staying competitive in the rapidly evolving interior door market. With technologies such as AI-driven design software and automated machining systems, companies can not only keep pace with demand but also push the boundaries of what is possible in door design. Investing in these technologies will empower businesses to meet the needs of modern consumers while also optimizing their operations for improved profitability and sustainability.
Leveraging Data Analytics for Enhanced Customer Insights in Door Sales
The interior door manufacturing industry is on the brink of a transformation, with data analytics leading the charge towards enhanced customer insights in door sales. As highlighted in the recent white paper on the smart lock industry, the integration of big data analytics allows businesses to better understand consumer behaviors and preferences, paving the way for more targeted marketing strategies. The increasing reliance on data-driven decisions is critical in an era where the majority of consumer interactions have shifted online.
In 2025, leveraging data analytics will be essential for manufacturers aiming to stay competitive. Industry analysts predict that the use of customer data will not only enhance sales strategies but also improve product development cycles. By analyzing purchase patterns and customer feedback in real time, businesses can tailor their offerings more precisely, responding to emerging trends and consumer demands. This proactive approach could result in significant market shares in the rapidly evolving door manufacturing sector.
Furthermore, as the digital landscape continues to evolve, companies that embrace data analytics will find themselves in a better position to capitalize on growth opportunities. The potential to predict market needs through the analysis of vast data sets opens new avenues for innovation in product design and functionality. For instance, manufacturers can utilize insights from customer interactions on e-commerce platforms to refine their product lines, ensuring they meet the contemporary expectations of quality and smart technology integration that consumers are increasingly seeking.