8 Essential Door Manufacturing Machines to Elevate Your Production Efficiency
In the competitive landscape of the manufacturing industry, enhancing production efficiency is paramount for any door manufacturing business aiming to thrive. The right set of tools can make all the difference, particularly when it comes to streamlining processes and improving the quality of the final product. This is where specialized Door Manufacturing Machines come into play. These advanced technologies not only speed up production times but also ensure that each door meets the highest standards of precision and durability.
From automated cutting systems to innovative assembly lines, a variety of machines exist to cater to the diverse needs of door production. In this blog, we will explore eight essential Door Manufacturing Machines that can significantly elevate your production efficiency. By integrating these machines into your workflow, you can optimize operations, reduce labor costs, and ultimately enhance your product offering, keeping your business ahead of the competition. Join us as we delve into the machinery that can transform your production capabilities and set a new standard in door manufacturing.
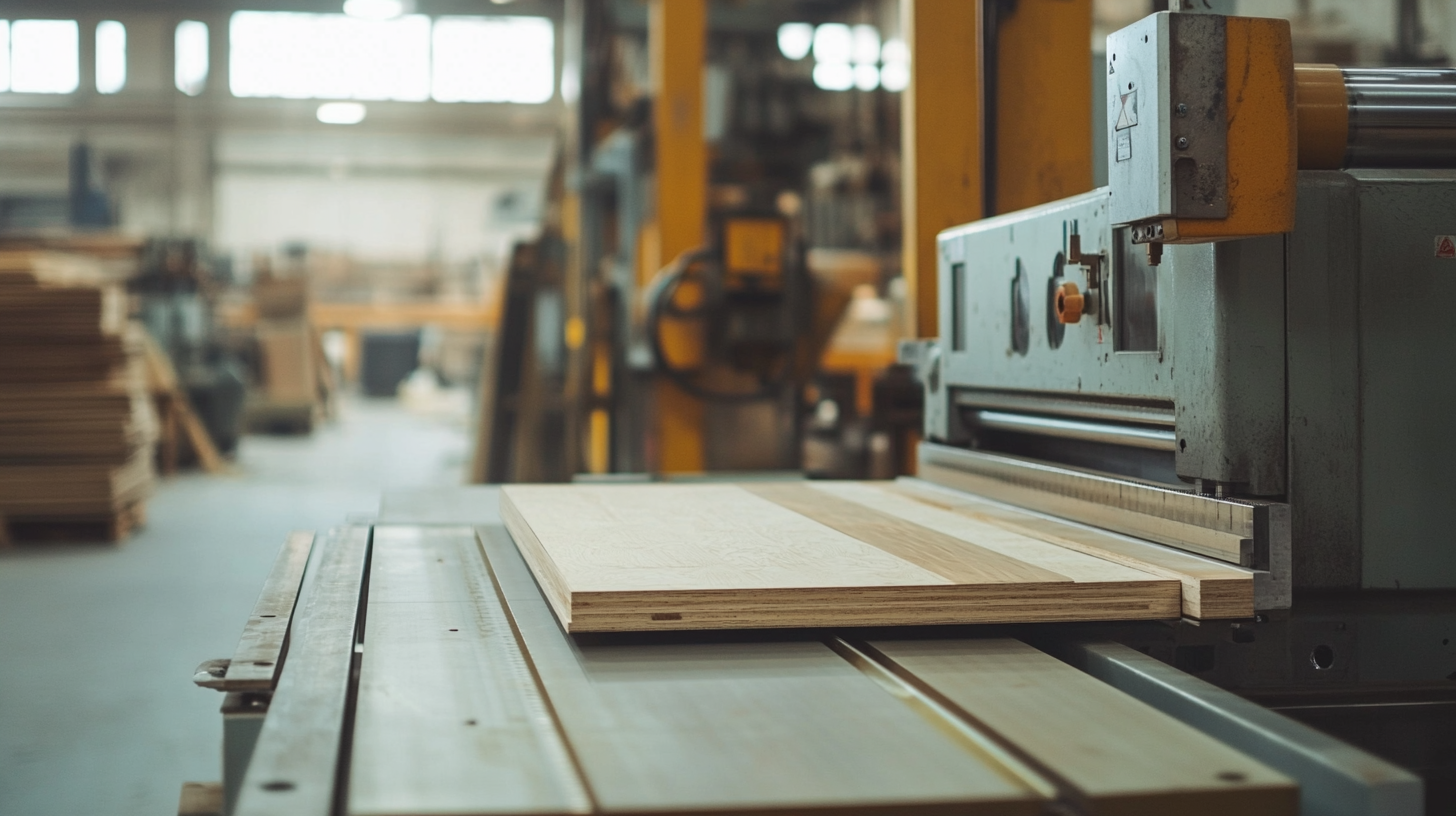
Choosing the Right Machinery for Door Production Efficiency
When selecting machinery for door production, the choice of equipment can significantly influence operational efficiency and overall product quality. According to a report from the Woodworking Network, the efficiency of manufacturing processes can be improved by as much as 30% with the right machinery selection. This means that not only does the choice of machines impact the speed of production, but it also affects material waste and labor costs, which are critical factors in maintaining a competitive edge in the industry.
For instance, investing in high-quality CNC routers can streamline the cutting process, allowing manufacturers to create complex designs with precision and minimal waste. Research from the Association of Woodworking & Furnishings Suppliers indicates that, with precise machinery, companies can expect to reduce material waste by approximately 15%. In addition, automated assembly lines equipped with advanced robotics can enhance production rates, allowing manufacturers to meet growing demand without compromising on quality.
Moreover, specialized machines for finishing processes can ensure a superior end product. A recent industry study highlighted that doors produced with automated finishing systems show a 25% improvement in finish consistency compared to manual methods. As the market continues to evolve, leveraging technology in door manufacturing not only enhances efficiency but also leverages data for further process optimization. Therefore, prioritizing the right machinery can lead to significant advancements in production efficiency and product quality in door manufacturing.
8 Essential Door Manufacturing Machines to Elevate Your Production Efficiency
This chart displays the effectiveness of various door manufacturing machines in enhancing production efficiency. Each machine is rated on a scale of 1 to 100 based on their impact on production time and quality.
Key Features to Look for in Door Manufacturing Machines
When exploring door manufacturing machines, it's essential to focus on key features that significantly enhance production efficiency. According to a report by MarketsandMarkets, the global door manufacturing equipment market is projected to reach USD 13.1 billion by 2025, indicating a robust demand driven by automation and technological advancements.
One of the primary features to consider is automation capabilities. Machines equipped with CNC (Computer Numerical Control) technology can optimize precision and reduce labor costs. A study published in the Journal of Manufacturing Science & Engineering revealed that CNC machines can improve production efficiency by up to 50%, allowing manufacturers to meet increasing demands without compromising quality. This is critical in an industry where customization and complexity are increasingly required.
Another vital aspect is the versatility of the machines. Multi-functional machines that can handle various materials, such as wood, metal, and composites, are invaluable in minimizing production downtime. A survey from the Woodworking Machinery Industry Association suggested that companies utilizing versatile machines reported a 30% increase in production time, enabling quicker adjustments to changing design trends and consumer preferences.
Lastly, energy efficiency should not be overlooked. Machines designed with energy-saving technologies can significantly reduce operating costs, contributing to a more sustainable production environment. The U.S. Department of Energy indicates that improving energy efficiency in manufacturing processes can result in energy savings of 20-30%, leading to not only cost savings but also a lowered environmental impact. Investing in door manufacturing machines with these essential features will undoubtedly elevate production efficiency and position businesses for future growth.
8 Essential Door Manufacturing Machines to Elevate Your Production Efficiency
Machine Type | Key Features | Efficiency Benefits | Investment Cost |
---|---|---|---|
CNC Router | Precision cutting, automated design integration | High accuracy, reduced waste | $30,000 - $100,000 |
Edge Banding Machine | Automatic gluing, trimming, and scraping | Streamlined finishing process | $25,000 - $70,000 |
Door Sanding Machine | Multi-head sanding, adjustable speed | Consistent surface finish | $20,000 - $60,000 |
Drilling Machine | Automated hole positioning, multiple drill heads | Fast drilling speed, higher output | $15,000 - $50,000 |
Press Machine | Hydraulic pressing, adjustable molding | Improved shaping accuracy | $35,000 - $90,000 |
Cutting Machine | Laser or saw cutting technology | High precision, complex designs | $25,000 - $75,000 |
Finishing Machine | Spray, UV curing, and varnishing features | Enhanced durability and aesthetics | $20,000 - $80,000 |
Assembly Line | Continuous flow setup, station automation | Increased throughput, reduced labor costs | $50,000 - $150,000 |
Essential Technologies for Streamlining Door Production Processes
In the competitive landscape of door manufacturing, implementing essential technologies is crucial for optimizing production processes. Recent industry reports indicate that manufacturers who invest in advanced machinery can boost their production efficiency by up to 30%. This enhances not only the speed of production but also the consistency and quality of the final product, critical attributes that customers seek.
One of the key technologies redefining the door manufacturing sector is the automated CNC machining center. This machine allows for precise cuts and designs that were previously only achievable through manual labor. According to a report by the Association of Woodworking and Furnishing Suppliers, companies that adopted CNC technology saw a reduction in production time by nearly 25%, enabling them to meet increasing consumer demands more effectively. Additionally, digitalization in machinery, such as smart saws and inline assembly systems, integrates flawlessly with CAD software, leading to reduced wastage and improved workflow.
Furthermore, incorporating lightweight materials and specialized finishing machines can significantly reduce lead times and enhance product durability. Data from the Wood Industry Market Report shows that the demand for energy-efficient and eco-friendly doors has surged, prompting manufacturers to upgrade their finishing techniques. Employing modern spraying technology ensures a superior finish while minimizing solvent usage, aligning production with environmental sustainability goals.
Overall, by embracing these essential technologies, door manufacturers can streamline their processes, improve output quality, and adapt to market trends efficiently. Investing in sophisticated machinery not only enhances capabilities but also positions companies as leaders in an ever-evolving industry.
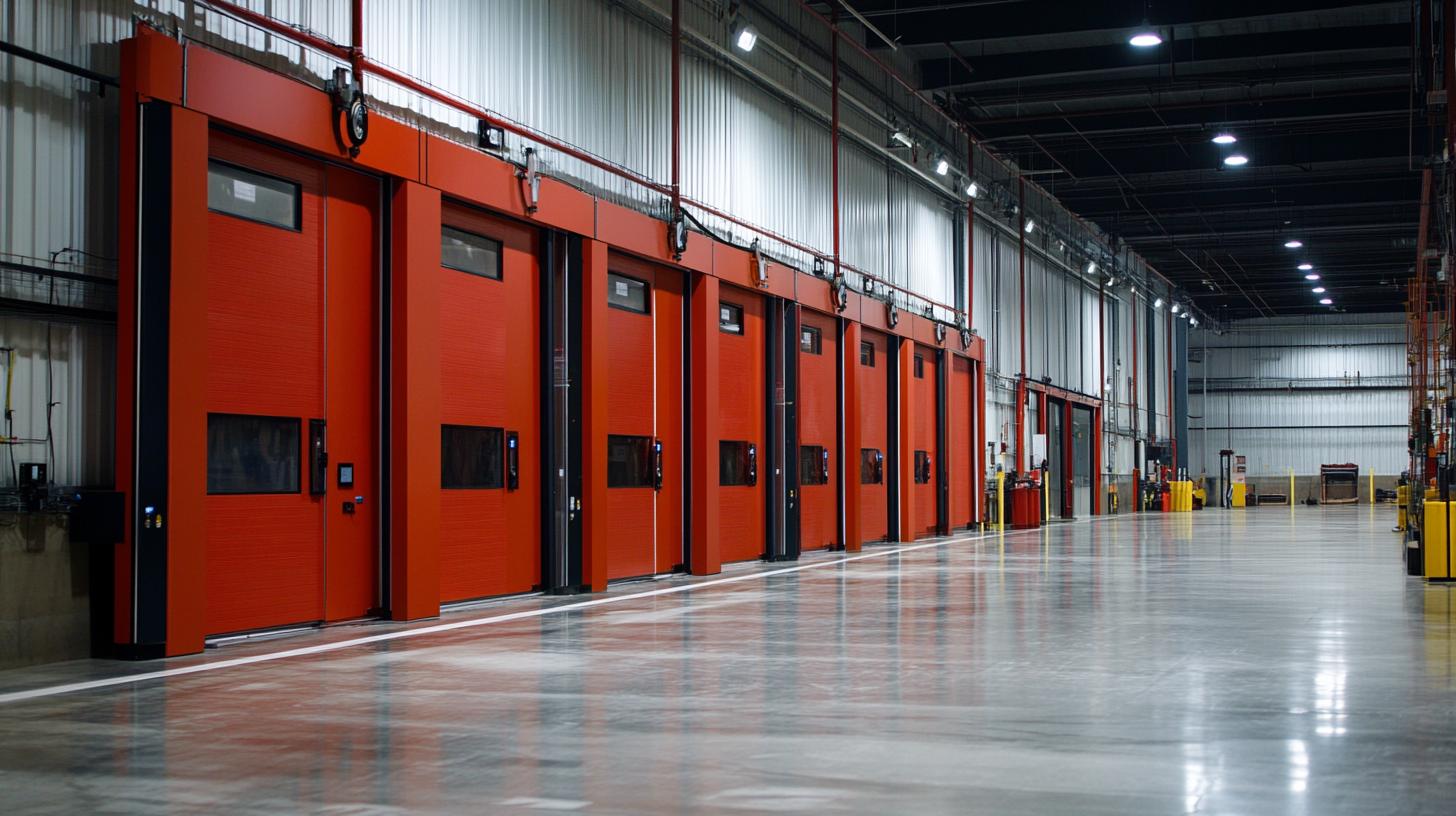
Maximizing Output: Best Practices for Integrating Machines
Integrating the right machines into your door manufacturing process is vital for maximizing production efficiency. First and foremost, consider the workflow layout of your facility. The strategic placement of machines can significantly reduce handling time and streamline operations. For example, arranging the CNC router, edge bander, and assembly station in a linear fashion minimizes unnecessary movement, enabling workers to focus on their tasks rather than navigating around obstacles.
Additionally, investing in machines that offer automation can greatly enhance output. Automated processes, like automatic sanding or painting systems, not only speed up production but also maintain consistent quality. It's crucial to train your staff on these machines to leverage their full potential. Understanding how to operate and maintain automation effectively can lead to fewer downtimes and increased productivity.
Implementing a system for regular maintenance and updates can also ensure your machinery operates at peak efficiency. Establishing a routine inspection schedule helps identify potential issues before they escalate, ultimately saving time and costs in the long run. By adopting these best practices in machine integration, door manufacturers can not only elevate their production efficiency but also stay competitive in a fast-paced market.
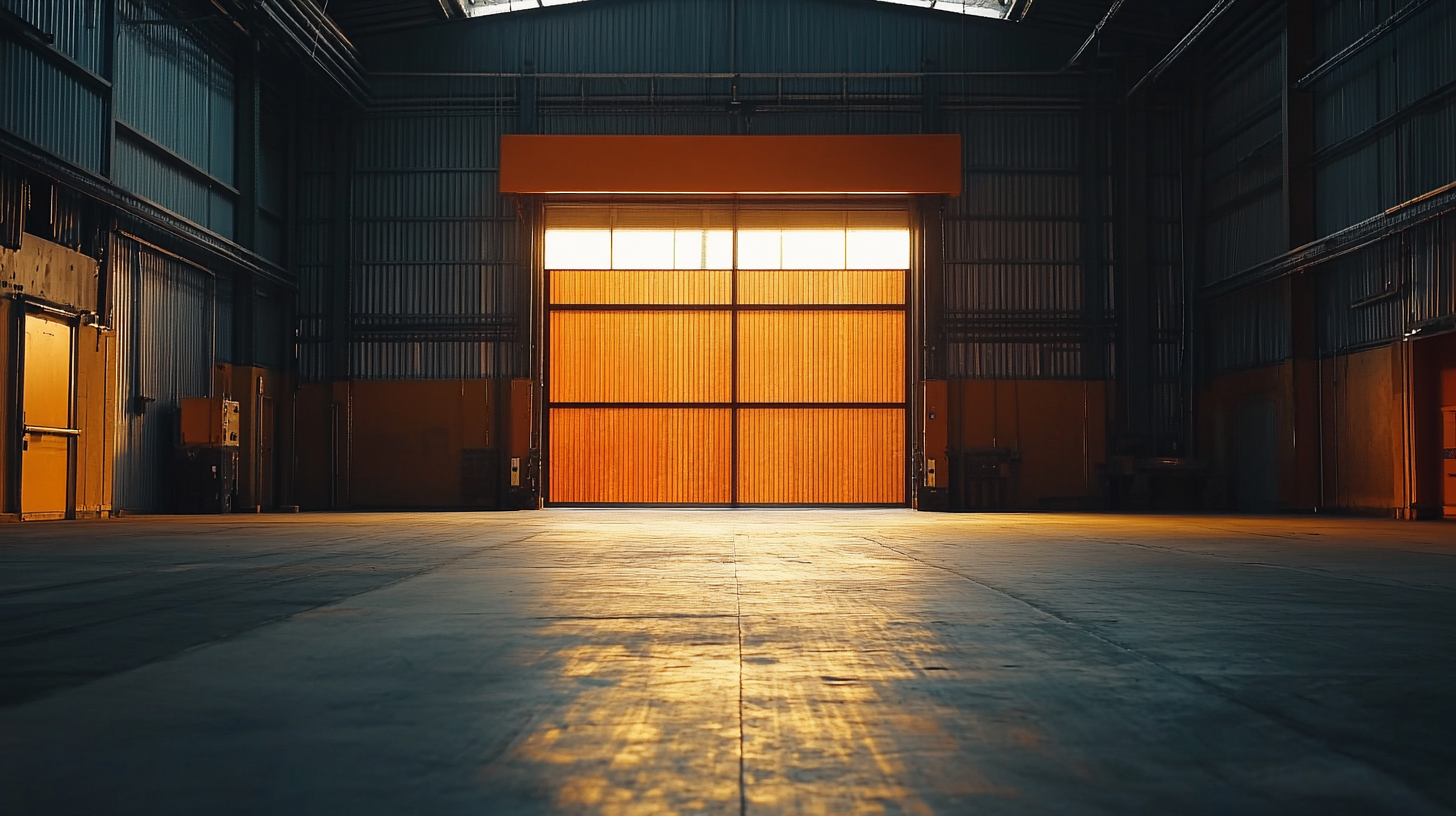
Maintaining Your Door Manufacturing Machines for Longevity and Efficiency
When it comes to door manufacturing, maintaining your machines is crucial not only for operational efficiency but also for extending their longevity. Regular maintenance schedules can significantly reduce unscheduled downtime, which industry reports indicate can cost manufacturers up to 5% of their annual revenue. By ensuring that machines are well-maintained, manufacturers can also enhance product quality, which in turn can lead to higher customer satisfaction and increased sales.
Routine checks, including lubrication of moving parts and calibration of cutting tools, are essential practices for door manufacturing equipment. According to a study by the Machinery Maintenance Association, preventative maintenance can increase a machine's lifespan by nearly 30%. Investing in proper maintenance protocols helps in avoiding costly repairs that may arise from neglect.
Furthermore, incorporating smart technology that monitors machine performance can help manufacturers catch problems early. An estimated 70% of machine failures are attributed to oversight in maintenance, highlighting the importance of systematic monitoring. By leveraging technology, manufacturers can ensure that their equipment operates at optimal levels, ultimately producing better quality doors in a more efficient manner. This not only saves costs but also boosts productivity, making maintenance an essential component of a successful door manufacturing operation.