Transform Your Production Line: Unleashing the Power of Innovative Casing Machines for Global Manufacturers
In today's fast-paced manufacturing environment, efficiency and adaptability are paramount for global manufacturers seeking to maintain a competitive edge. The increasing demand for customized packaging solutions and streamlined operations has put a spotlight on advanced machinery, particularly Casing Machines. According to a report by Smithers, the global packaging machinery market is projected to reach $50 billion by 2024, with Casing Machines playing a critical role in meeting the needs of diverse industries, including food, beverage, pharmaceuticals, and consumer goods. These innovative machines not only enhance production speed but also improve packaging accuracy and reduce material waste.
As manufacturers strive for automation and agility in their production lines, the integration of cutting-edge Casing Machines has become a game-changer. A study by MarketsandMarkets indicates that the automation in manufacturing is expected to grow at a CAGR of 9% from 2021 to 2026, with packaging automation being a significant contributor. By investing in state-of-the-art Casing Machines, companies can ensure operational efficiency, higher product quality, and lower labor costs. Embracing these advancements allows manufacturers to adapt swiftly to market demands, ultimately transforming their production lines into agile, sustainable operations ready to meet the challenges of the global marketplace.
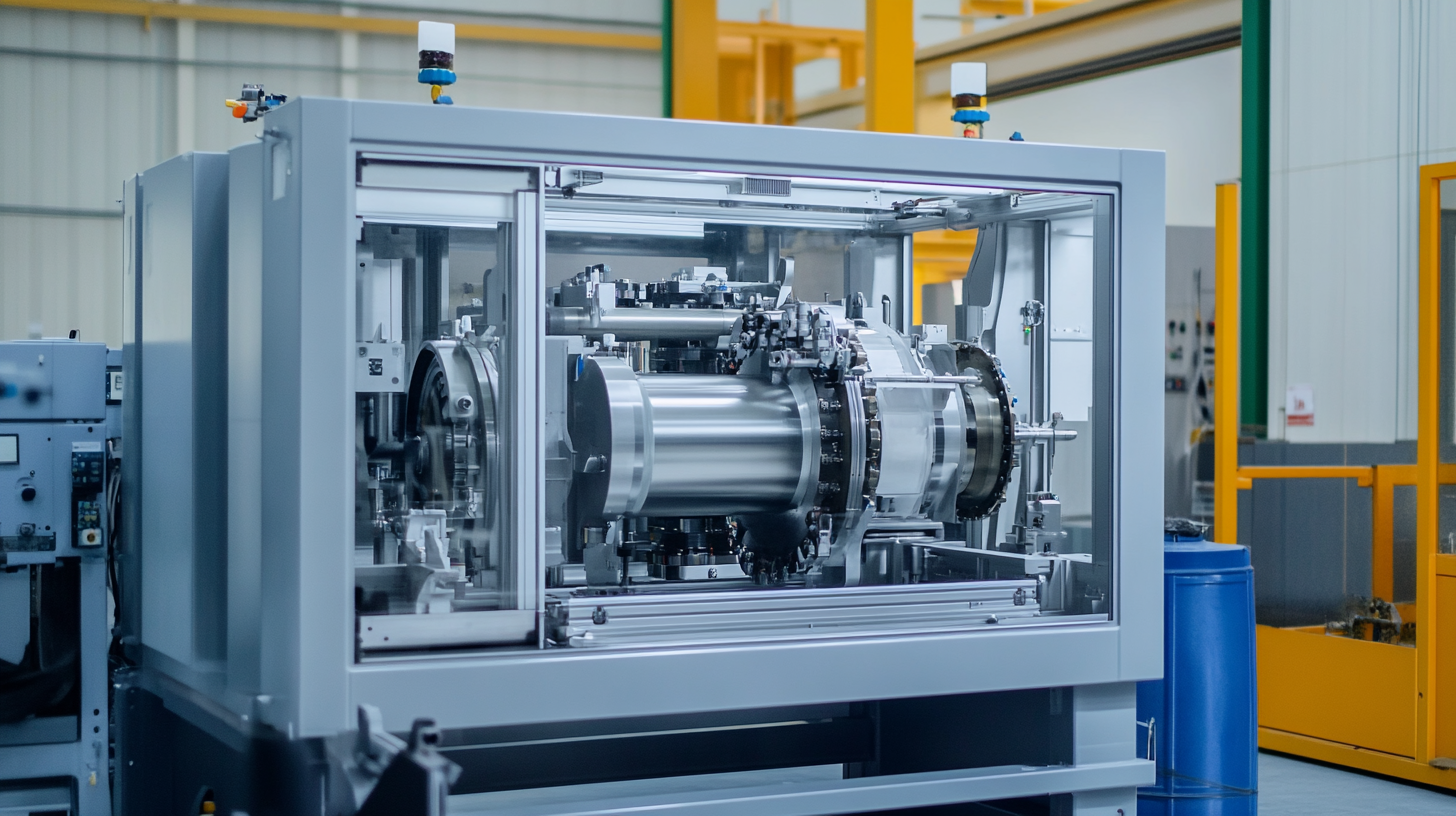
The Impact of Innovative Casing Machines on Production Efficiency in Manufacturing
In the fast-paced world of manufacturing, efficiency is the key to staying competitive. Innovative casing machines have emerged as a game-changer, significantly boosting production efficiency across various industries. These advanced machines streamline the packaging process, minimizing downtime and maximizing output. By automating complex tasks that were once manual, manufacturers can focus their efforts on core operations while ensuring consistent quality and speed in their production lines. The integration of innovative casing machines also enhances flexibility in manufacturing. With advanced technology, these machines can easily adjust to different product sizes and packaging styles, allowing manufacturers to respond swiftly to market demands. This adaptability not only improves the overall workflow but also reduces waste and lowers operational costs. In an era where consumer preferences shift rapidly, having this agility can make a substantial difference in maintaining market relevance and customer satisfaction. Moreover, the use of innovative casing machines contributes to a more sustainable production environment. By optimizing material usage and improving energy efficiency, manufacturers can significantly reduce their ecological footprint. As companies increasingly prioritize sustainability, adopting advanced packaging solutions showcases a commitment to responsible manufacturing practices. Ultimately, the impact of these innovative machines transcends mere efficiency; they pave the way for a more agile, cost-effective, and environmentally friendly manufacturing process.
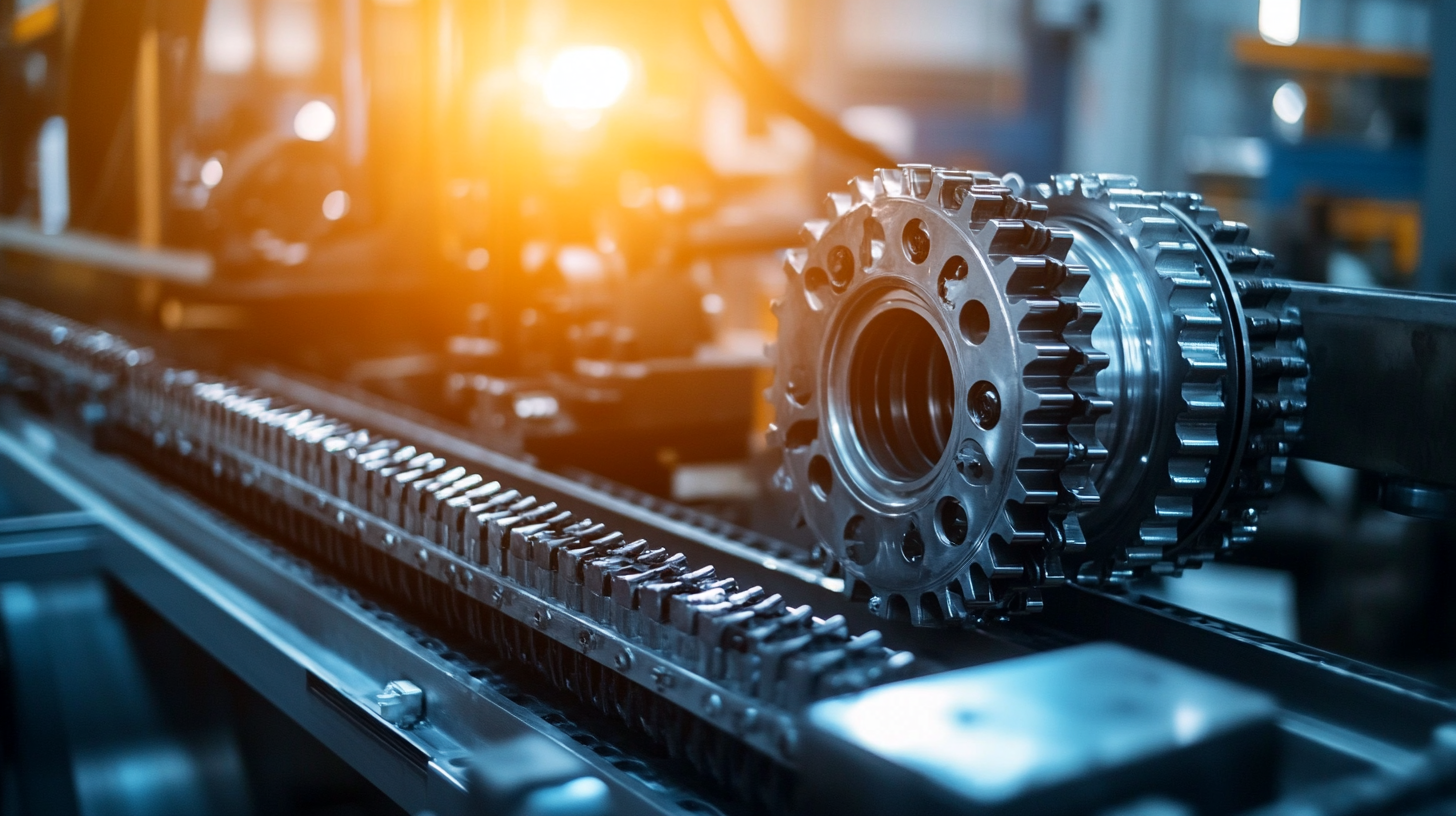
Key Trends in Casing Machine Technologies Transforming Global Supply Chains
In recent years, the packaging industry has witnessed a significant technological shift, particularly in the domain of casing machines. According to a report by Smithers Pira, the global market for packaging machinery is projected to reach $47.4 billion by 2024, driven by innovations that enhance efficiency and sustainability. The emergence of smart casing machines has been a game-changer for manufacturers looking to streamline operations and reduce waste throughout the supply chain.
One of the key trends redefining casing machine technology is the integration of Industry 4.0 principles. Modern machines are now equipped with IoT capabilities, enabling real-time monitoring and data analytics. This shift not only improves transparency across global supply chains but also allows for predictive maintenance, reducing downtime by up to 20% as noted in a recent report by Deloitte. Manufacturers leveraging these advanced technologies can respond more rapidly to market demands, ensuring their operations remain flexible and competitive.
Furthermore, the push for sustainability in packaging is prompting advancements in casing machine design. According to the Ellen MacArthur Foundation, adopting circular economy principles could generate $4.5 trillion in economic benefits by 2030. Innovative casing machines that utilize recyclable materials or significantly reduce material waste are becoming vital. For example, new designs can minimize the use of plastics while maintaining product integrity, aligning with consumer demands for environmentally responsible packaging solutions. As manufacturers embrace these advancements, the potential for a transformative impact on global supply chains becomes increasingly apparent.
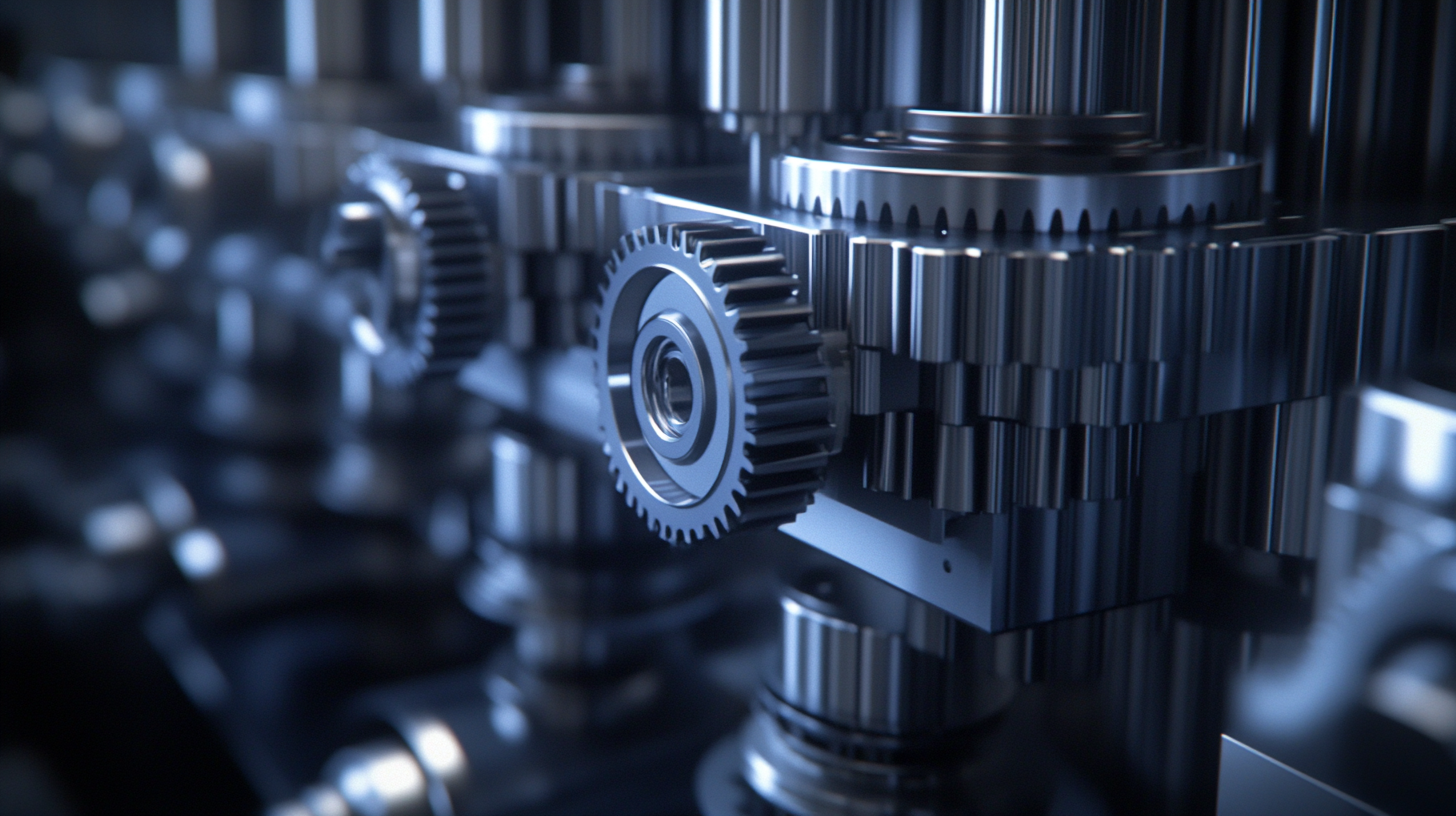
Case Studies: Success Stories of Manufacturers Adopting Advanced Casing Solutions
In the rapidly evolving landscape of manufacturing, turning to advanced casing solutions has emerged as a game-changer for many global manufacturers. By adopting innovative casing machines, companies not only streamline their production processes but also enhance product quality and reduce operational costs. Case studies reveal a plethora of success stories where manufacturers implementing new casing technologies have experienced significant boosts in efficiency.
For instance, a leading manufacturer in the food sector reported a 30% increase in production rates after integrating automated casing machines. This approach not only accelerated their output but also improved consistency in packaging quality, which is crucial for meeting consumer expectations. Similarly, in the electronics industry, a manufacturer that transitioned to IoT-enabled casing solutions experienced a 25% reduction in material waste, further emphasizing the role of technology in optimizing production lines.
The positive trend in case studies aligns with recent reports highlighting the effectiveness of IoT initiatives. An astounding 92% of enterprises revealed they achieved a positive ROI from their IoT implementations, signaling a widespread recognition of technology's potential to drive efficiency and profitability in manufacturing processes. As manufacturers increasingly adopt advanced technologies, it's clear that the benefits of innovative casing solutions will continue to revolutionize the industry, setting new standards for performance and quality.
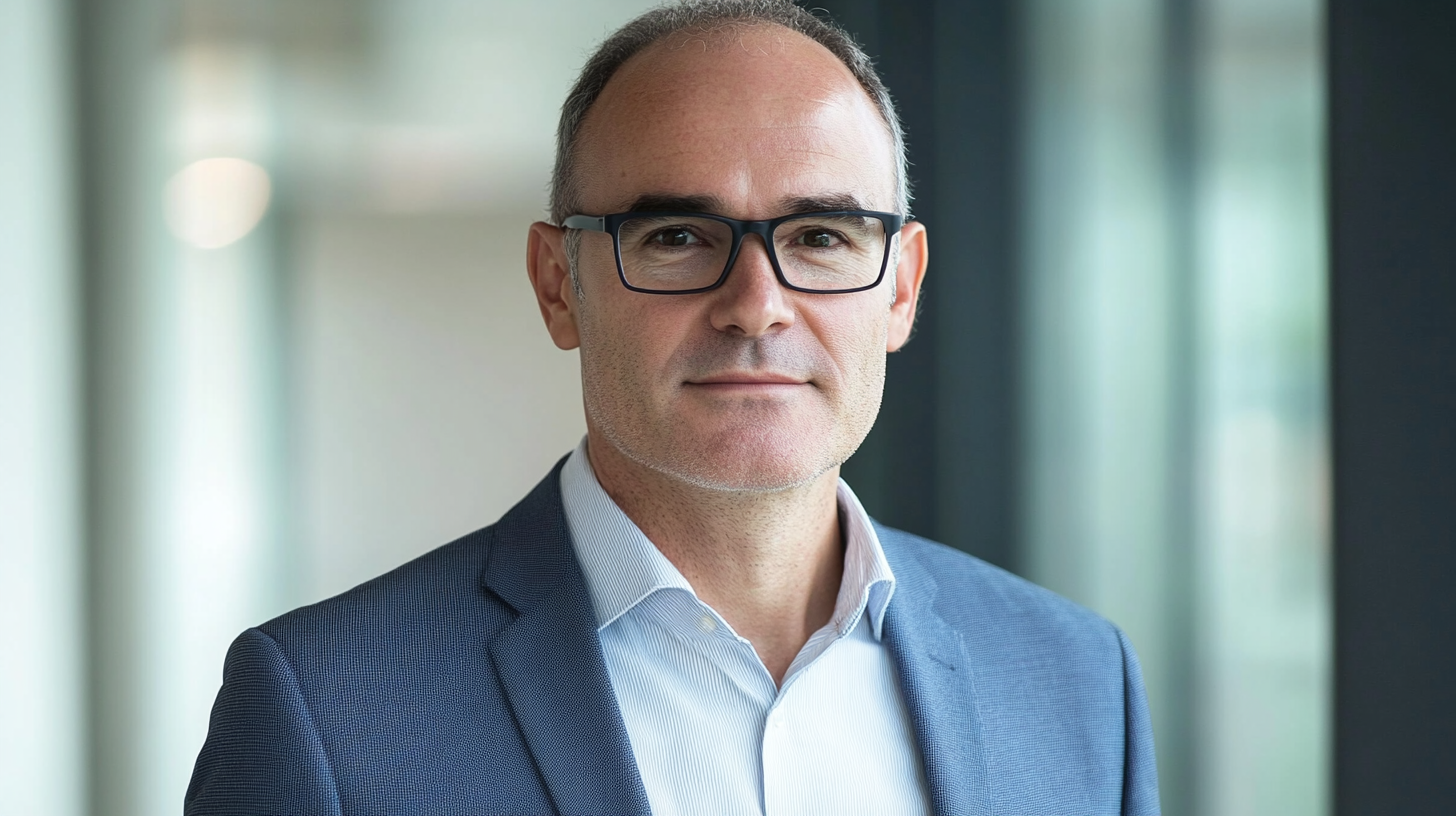
Analyzing Cost Savings: How Modern Casing Machines Reduce Operational Expenses
In today’s rapidly evolving manufacturing landscape, modern casing machines are redefining operational efficiency and cost management. According to industry reports, the implementation of innovative casing technologies can lead to significant reductions in operational expenses, with savings often reaching up to 30% in some manufacturing environments. This cost-effectiveness stems from enhanced automation, which minimizes labor costs and reduces material waste, ultimately driving down the overall cost of production.
Furthermore, the global trend towards smarter logistics solutions reinforces this transition. By 2027, initiatives across various regions are expected to lower logistics costs significantly, targeting an overall reduction in the logistics-to-GDP ratio to approximately 12%. This strategic goal aligns with the ongoing push for digital transformation within the logistics sector, enhancing inventory management and streamlining supply chain processes. These advancements not only support manufacturers in reducing costs but also enable them to respond more quickly to market demands.
The investment in advanced casing machinery, therefore, is not merely an operational upgrade; it is a strategic imperative for manufacturers who wish to stay competitive in a cost-sensitive marketplace. As the industry moves towards greater precision and efficiency, investing in modern equipment becomes a crucial factor in achieving sustained economic viability and growth.
Future Predictions: The Role of Automation in Casing Machine Development and Usage
As the manufacturing landscape evolves, the integration of automation within casing machines is poised to play a pivotal role in enhancing production efficiencies. Future predictions suggest that advancements in artificial intelligence (AI) will drastically reshape the development and usage of these machines. Automation not only streamlines the packaging process but also introduces a level of precision previously unattainable, reducing waste and improving product quality.
AI is revolutionizing the manufacturing industry through applications such as predictive maintenance and supply chain optimization. Casing machines equipped with AI capabilities can adapt to changing conditions in real-time, ensuring optimal performance and minimizing downtime. Manufacturers are increasingly leveraging smart technologies to predict when a machine might fail, allowing for timely interventions that enhance productivity and efficiency.
The economic potential of automation and generative AI in production lines is substantial. As companies worldwide seek to harness these powerful tools, the case for investing in innovative casing machines becomes compelling. The future path of manufacturing lies in the ability to adapt quickly to market demands while ensuring consistent quality, and automation technologies will be at the forefront of this transformation. With generative AI driving new applications and capabilities, the coming years may see unprecedented advancements in how products are packaged and delivered globally.