Unlocking the Potential of Interior Door Machines with Key Technical Specifications and Best Practices
The interior door manufacturing industry is experiencing significant transformation, driven by advancements in technology and an increasing demand for efficiency and precision. According to a recent report from MarketsandMarkets, the global market for woodworking machinery, including Interior Door Machines, is projected to reach USD 12.5 billion by 2025, growing at a compound annual growth rate (CAGR) of 5.3%. This surge highlights the pivotal role that specialized machinery plays in enhancing productivity and ensuring high-quality output within the competitive landscape of interior door production.
To fully capitalize on this growth, manufacturers must focus on understanding the key technical specifications and best practices associated with Interior Door Machines. These machines not only streamline the manufacturing process but also contribute to the customization and versatility that modern consumers demand. As noted by the International Woodworking Fair, integrating cutting-edge technologies such as automation and CNC capabilities allows manufacturers to optimize their workflows and reduce lead times while maintaining craftsmanship quality. This blog will delve into the essential features and operational insights that can unlock the full potential of Interior Door Machines, positioning manufacturers to thrive in a rapidly evolving market.
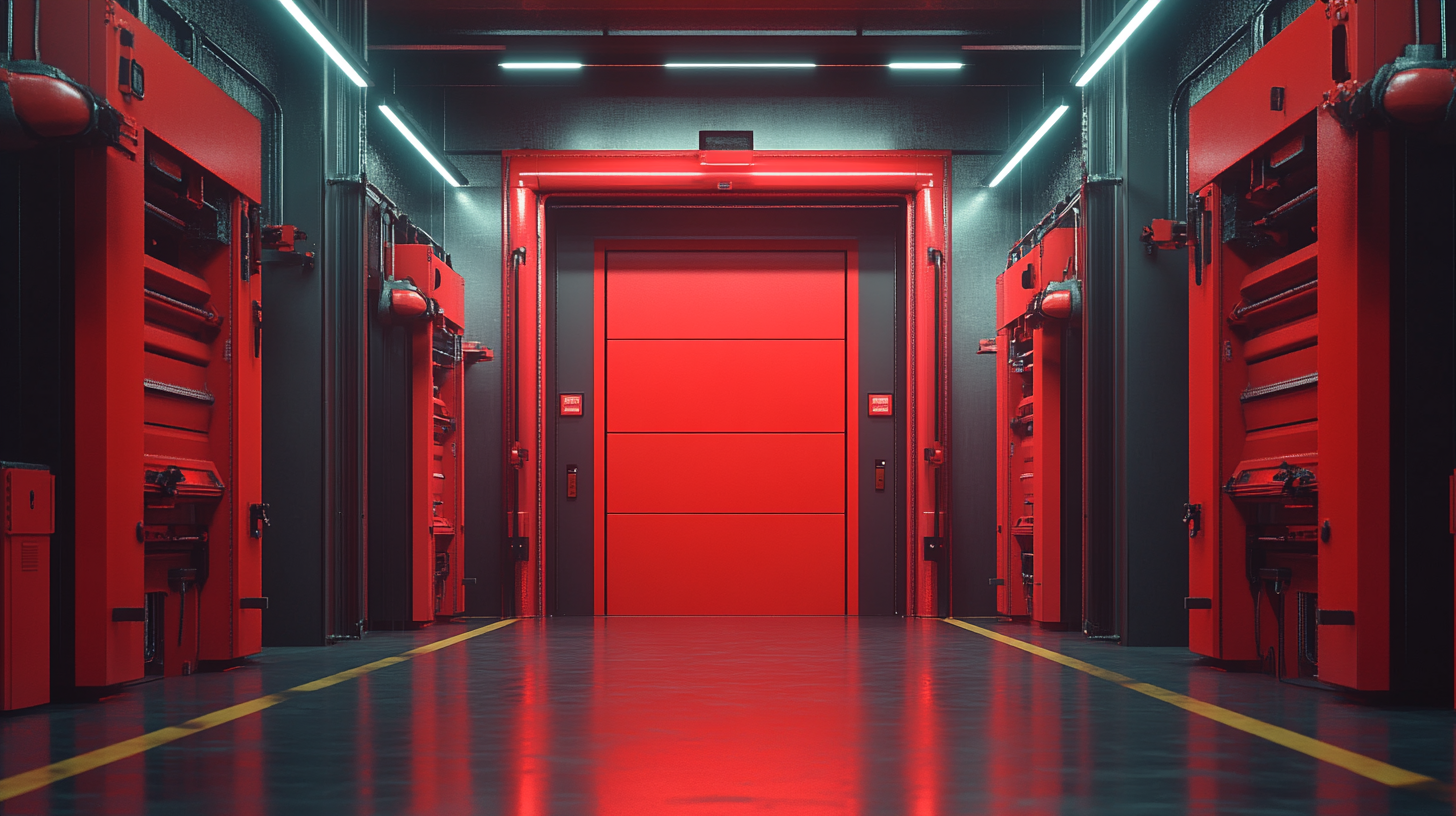
Understanding the Key Technical Specifications of Interior Door Machines
When it comes to manufacturing interior doors, understanding the key technical specifications of interior door machines is crucial for optimizing performance and efficiency. These machines are designed to execute a variety of processes, including cutting, shaping, and assembling door components. Each specification, from power consumption to cutting speed, plays a vital role in determining the quality and consistency of the final product. One of the most important specifications is the machine's cutting precision. A precise cutting capability ensures that doors fit perfectly within their frames, reducing the need for additional adjustments during installation. Furthermore, the type of blades used can significantly affect the smoothness of the cut, impacting the overall aesthetic of the door. It's essential to choose machines equipped with high-quality blades that can maintain sharpness over extended periods, minimizing downtime for maintenance. Another critical aspect is the feed rate, which influences how quickly materials are processed. A higher feed rate can improve productivity, but it must be balanced with the quality of the cut. Operators should select machines with adjustable feed rates to cater to various door sizes and types, ensuring optimal efficiency without sacrificing precision. By understanding these key technical specifications, manufacturers can make informed decisions that enhance their production capabilities and meet the evolving demands of the market.
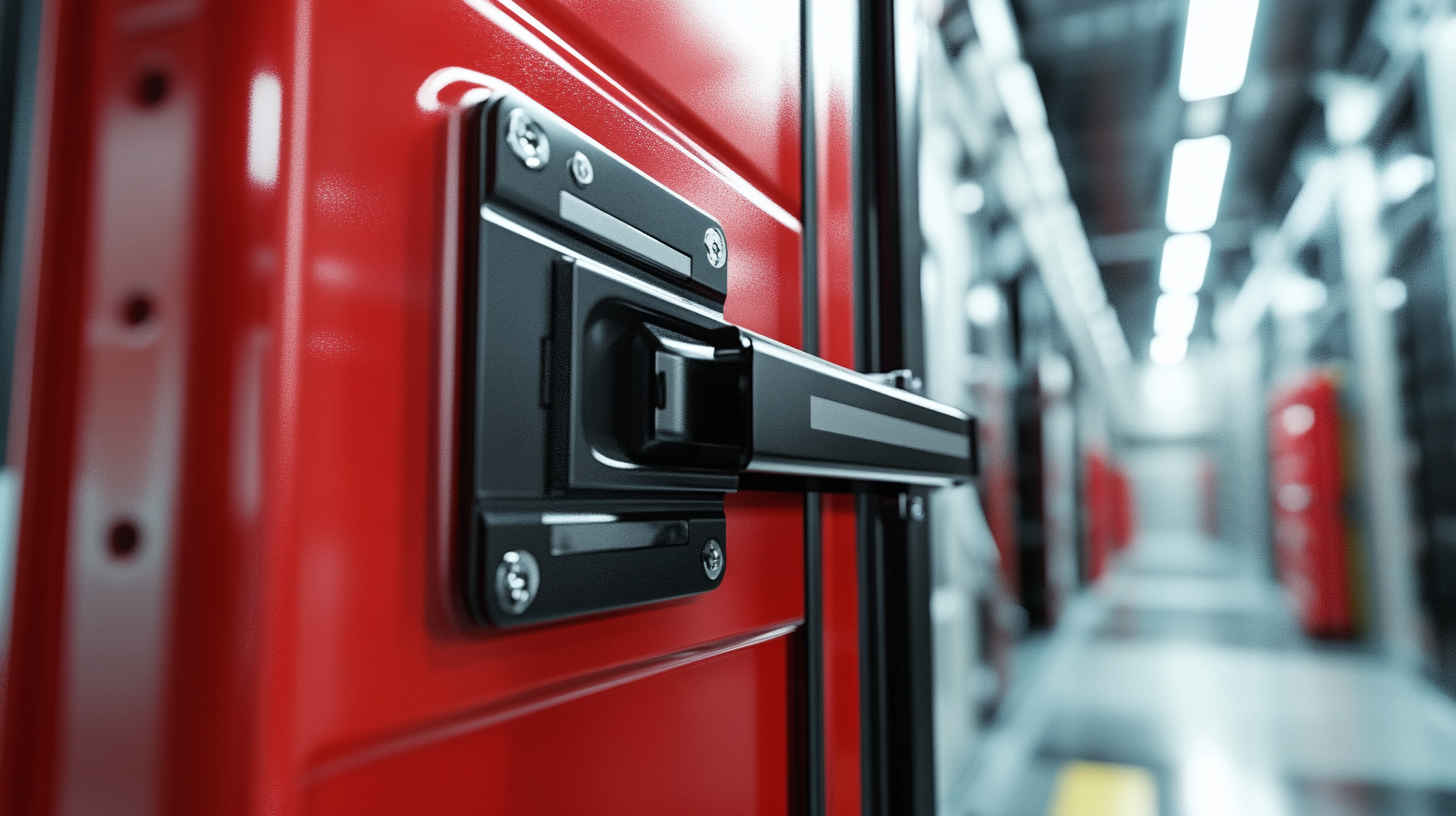
Essential Features to Look for in Modern Door Fabrication Equipment
When investing in modern door fabrication equipment, understanding the essential features can make all the difference in achieving efficiency and quality in production. First and foremost, precision is crucial; look for machines that offer advanced automation and software integration. These technologies not only streamline the cutting and shaping processes but also minimize human error, ensuring that each door is manufactured to exact specifications. Features like CNC (Computer Numerical Control) capabilities can enhance accuracy and repeatability, allowing for high-volume production without sacrificing quality.
Another critical aspect to consider is the adaptability of the door machines. Modern equipment should be versatile enough to handle a variety of door styles and materials, from solid wood to composite and hollow core doors. This flexibility enables manufacturers to respond to changing market demands and customer preferences without the need to invest in multiple machines. Additionally, machines equipped with quick-change tooling systems can significantly reduce downtime, allowing for quicker transitions between different production setups.
Lastly, examining the energy efficiency and sustainability features of door fabrication equipment is increasingly important in today’s eco-conscious market. Machines designed with energy-saving technologies not only reduce operational costs but also align with environmental standards and practices. Features such as low power consumption, recyclable components, and minimal waste generation can enhance a company's reputation while contributing to a more sustainable future in manufacturing. Selecting the right combination of these essential features will ultimately unlock the full potential of interior door machines, setting businesses up for long-term success.
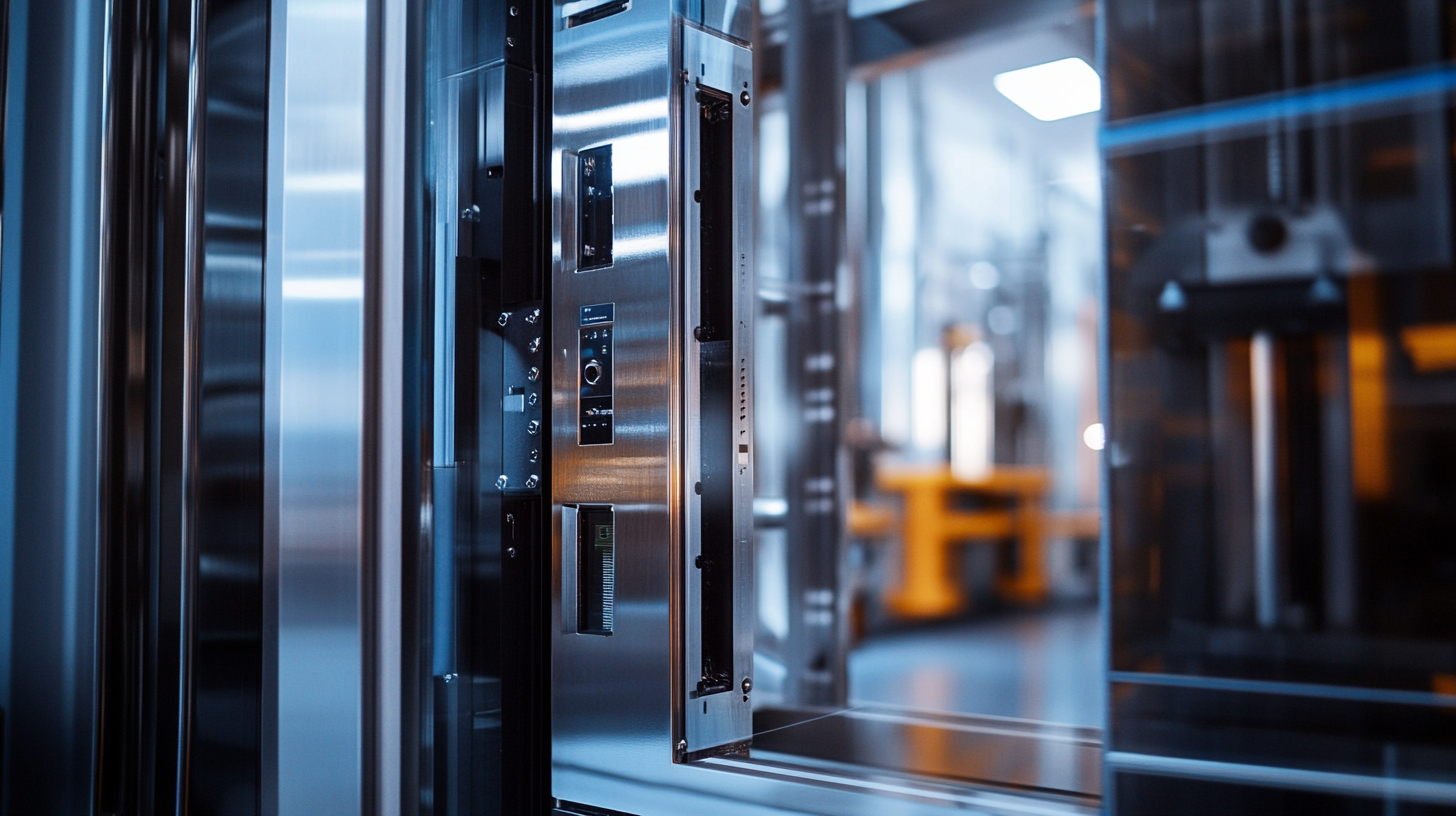
Best Practices for Maximizing Efficiency in Door Manufacturing
In the competitive landscape of door manufacturing, efficiency is paramount. Implementing best practices can significantly streamline operations and enhance productivity. One effective strategy is the optimization of workflow within the manufacturing process. This involves meticulous planning of each stage—from raw material procurement to assembly—ensuring that each step seamlessly transitions to the next. By creating a well-coordinated schedule and layout, manufacturers can minimize downtime and wasted movement, ultimately leading to faster production times.
Another critical aspect of maximizing efficiency is investing in advanced technology and machinery tailored for door manufacturing. Machines equipped with cutting-edge software can automate tedious tasks, reduce human error, and improve precision. Regular maintenance and timely upgrades of these machines are essential to prevent unexpected breakdowns and ensure consistent performance. Furthermore, training staff to utilize these technologies effectively can enhance their skills and confidence in handling sophisticated equipment.
Lastly, embracing lean manufacturing principles can drive significant improvements in efficiency. This methodology focuses on eliminating waste, whether it be in materials, time, or labor. By actively engaging employees in identifying inefficiencies and suggesting improvements, companies foster a culture of continuous improvement. Regularly reviewing processes and setting measurable goals will not only boost productivity but also create a more agile manufacturing environment, better equipped to respond to market demands.
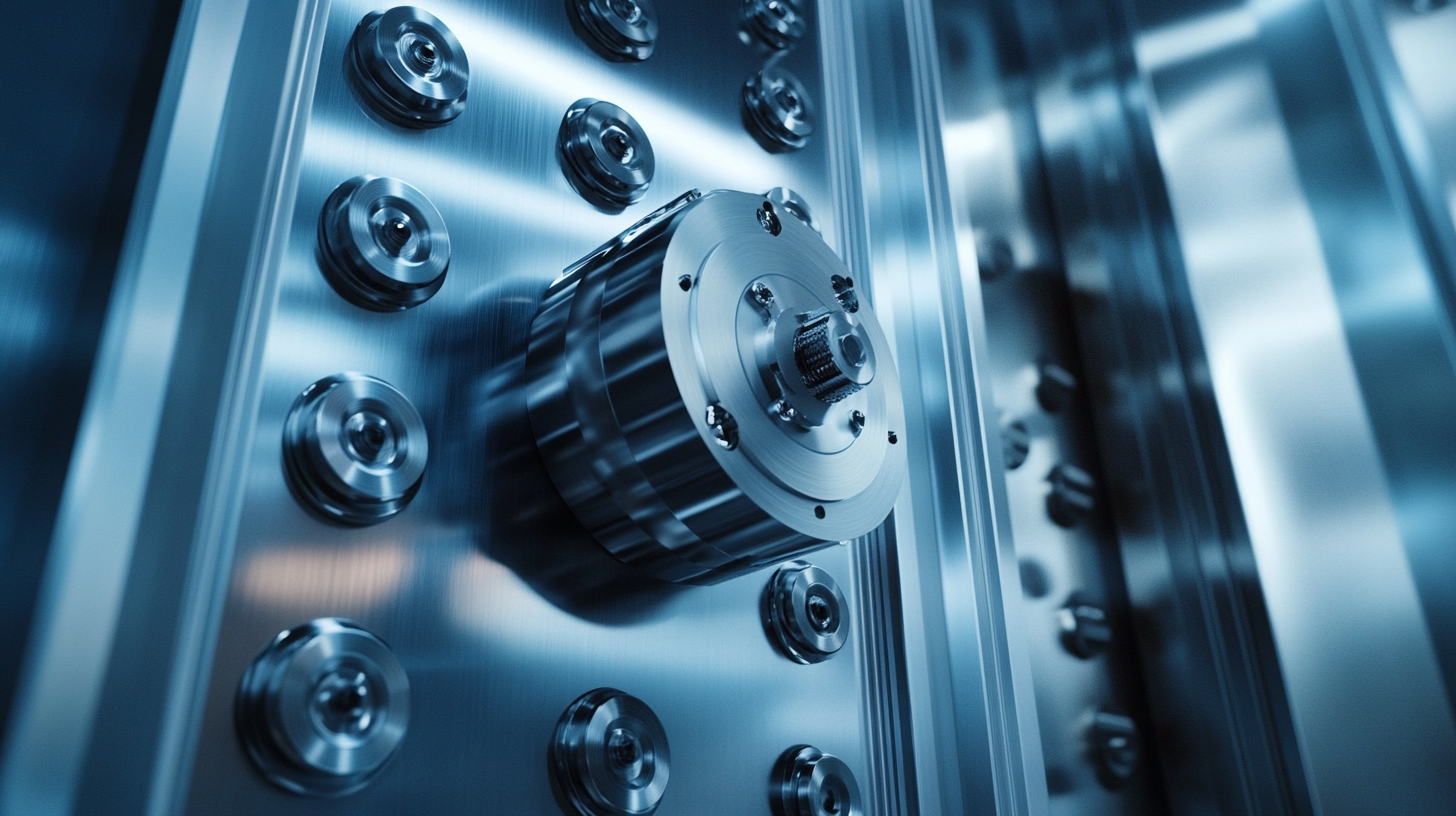
Common Challenges in Interior Door Production and How to Overcome Them
Production of interior doors presents several challenges that can hinder efficiency and product quality. One common issue is the inconsistency in material specifications, which can lead to variations in finished products. To address this, manufacturers should standardize their material sourcing and establish strict quality control protocols. This ensures that every batch of materials meets the required specifications, minimizing defects and rework.
Another significant challenge is the complexity of the production process itself. With multiple tasks involving cutting, machining, and finishing, the potential for bottlenecks increases. Implementing automated interior door machines can streamline operations, as they are designed to handle various tasks with precision and speed. Regular maintenance of these machines is also crucial; it helps prevent breakdowns and keeps production on schedule.
Training staff on best practices is vital to overcoming challenges in interior door production. Workers should be equipped with the necessary skills to operate machinery effectively and recognize potential problems before they escalate. By fostering a culture of continuous learning and improvement, manufacturers can enhance productivity and ensure superior quality in their interior door offerings.
Innovations in Technology That Are Shaping the Future of Door Machines
Innovations in technology are set to redefine the capabilities of interior door machines, unlocking their potential for enhanced production efficiency and precision. Recent industry reports indicate that the global market for door machines is anticipated to grow significantly, driven by advancements in automation, AI integration, and digital manufacturing techniques. As manufacturers increasingly adopt smart technologies, the focus is shifting towards machines equipped with real-time data processing capabilities, which allow for improved decision-making and operational efficiency.
One significant trend includes the incorporation of non-invasive brain-computer interface technologies, which demonstrate a practical application of futuristic concepts in manufacturing environments. These technologies not only enhance user interaction but also facilitate seamless control of machinery, potentially leading to unparalleled efficiency in the production line. By harnessing such innovations, interior door machines can significantly reduce production times while maintaining high-quality standards.
Moreover, advancements in laser technology and all-color display systems are enabling manufacturers to achieve greater levels of customization and precision. As reported by industry leaders, the implementation of these technologies enhances not only the aesthetic appeal of interior door designs but also provides robust manufacturing solutions that cater to specific market demands. The integration of AI-driven robotics further streamlines processes, allowing for adjustments in real-time and fostering a more responsive manufacturing environment.
In summary, the intersection of digital technology and traditional manufacturing practices is catalyzing a transformation in how interior door machines operate, shaping a future that is not only more efficient but also more adaptable to the evolving needs of the industry.