Unlocking Efficiency with the Best Casing Machines and Their Impact on Production Metrics
In today's fast-paced manufacturing landscape, the efficiency of production processes has become paramount, particularly for industries reliant on Casing Machines. According to a recent report by Smith & Associates, optimizing machinery performance can result in a productivity boost of up to 30%, significantly impacting overall production metrics. Casing Machines, essential for packaging and protecting products, not only enhance safety and convenience but also contribute to reducing operational costs. Moreover, effective after-sales services and maintenance strategies can lower repair costs by approximately 15%, as reported by the Manufacturing Efficiency Institute. By investing in high-quality Casing Machines and implementing robust support systems, businesses can unlock substantial operational efficiencies, ensuring they stay competitive in an ever-evolving market.
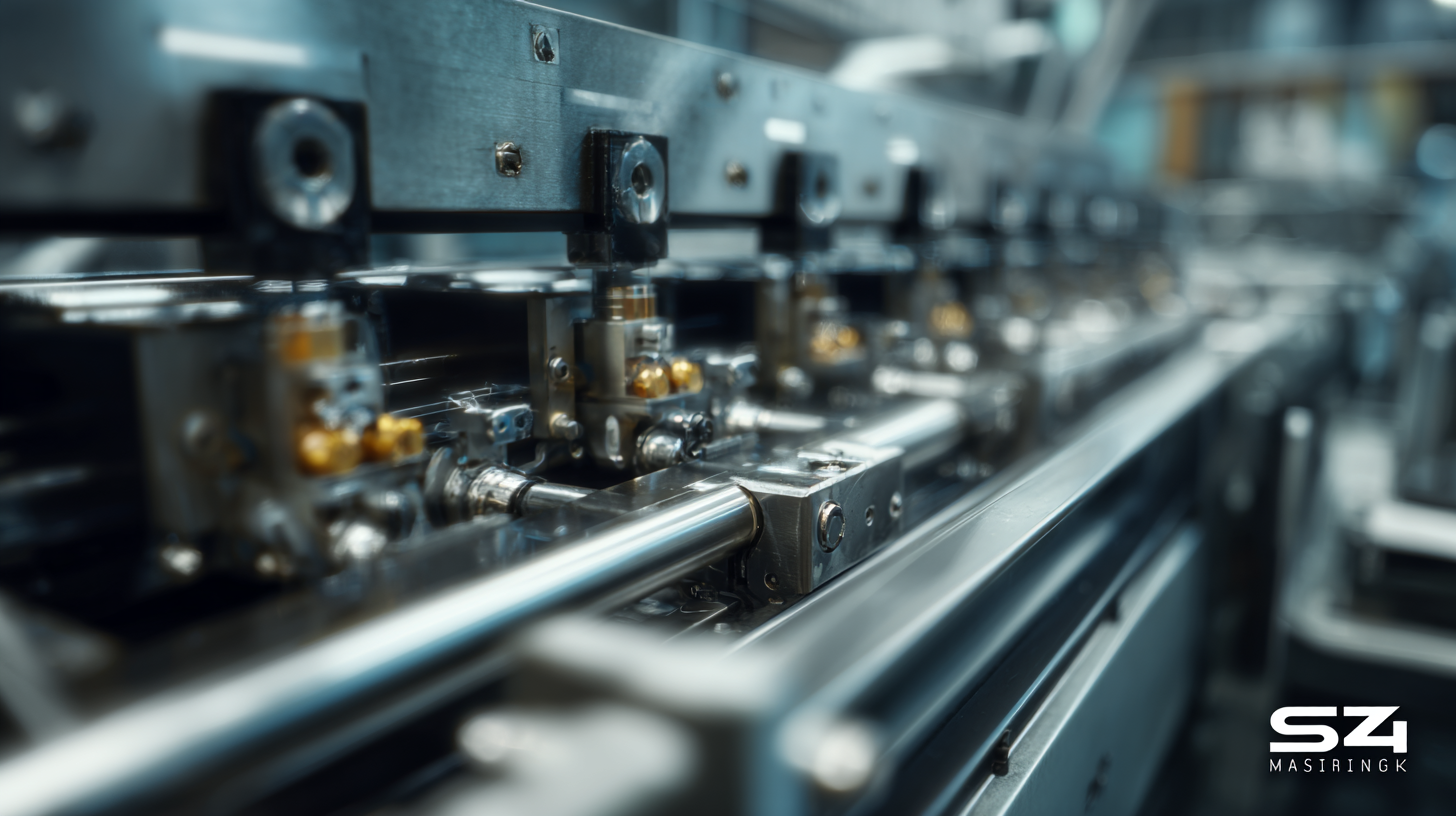
Understanding Casing Machines: An Overview of Types and Functions
Casing machines play a pivotal role in the packaging industry, streamlining operations and enhancing production efficiency. By categorizing casing machines into various types—such as automatic, semi-automatic, and manual—it’s crucial to understand their distinct functions and applications. Automatic casing machines, for instance, can significantly reduce labor costs and human error, leading to faster turnaround times and higher output volumes. According to industry reports, companies utilizing advanced casing technologies can see productivity improvements of up to 30%, demonstrating how vital these machines are in meeting market demands.
Moreover, the integration of advanced technologies such as machine learning and artificial intelligence into casing machinery is reshaping operational capabilities. These technologies enable predictive maintenance and real-time monitoring, further optimizing performance. A recent study highlighted that implementing AI in manufacturing processes could potentially add trillions of dollars in economic value worldwide. As industries continue to evolve, understanding the capabilities of different casing machines and leveraging innovative technologies will be essential for companies aiming to enhance their production metrics and remain competitive in the marketplace.
Key Features of High-Quality Casing Machines Enhancing Production Efficiency
In today’s fast-paced manufacturing landscape, high-quality casing machines play a pivotal role in enhancing production efficiency. According to a recent report by Grand View Research, the global market for packaging machinery is projected to reach $60 billion by 2027, driven in part by advancements in automation and technology. These state-of-the-art casing machines are designed not only for speed but also for precision, minimizing material wastage and ensuring consistent product quality. Features such as automated adjustments and real-time monitoring capabilities significantly reduce downtime, allowing manufacturers to respond promptly to changing production demands.
Additionally, the integration of smart technologies, such as IoT connectivity, enables casing machines to provide valuable data insights. A study by MarketsandMarkets highlights that companies employing analytics in their production processes can increase operational efficiency by up to 30%. With features like predictive maintenance and machine learning algorithms, today's casing machines proactively identify potential issues before they become costly breakdowns. By investing in high-quality casing machines equipped with these innovative features, manufacturers can not only boost their production metrics but also secure a competitive advantage in a rapidly evolving market.
The Role of Automation in Streamlining Casing Processes
In today’s fast-paced manufacturing environment, automation is transforming the casing processes, significantly enhancing productivity and efficiency. By integrating advanced casing machines, companies can streamline the packing workflow, reducing the time and labor required for traditional methods. Automated casing solutions facilitate consistent and precise packing, ensuring that every product is handled with care and precision, which minimizes waste and errors.
Moreover, the adoption of automation in casing processes allows for improved production metrics. These machines are designed to work seamlessly with existing production lines, increasing throughput without compromising quality. Real-time data monitoring and machine learning algorithms optimize performance by adjusting operational parameters on-the-fly, further driving efficiency. As a result, businesses not only achieve better output but also gain valuable insights into their production processes, enabling them to make informed decisions for continuous improvement.
Unlocking Efficiency with Casing Machines
Impact of Casing Machine Technology on Product Quality and Consistency
In today's competitive manufacturing environment, the importance of casing machine technology cannot be overstated. These machines play a pivotal role in enhancing product quality and ensuring consistent results across production lines. By automating the casing process, manufacturers can reduce human error while maintaining high standards for product presentation and safety. This efficiency not only elevates the final product but also boosts consumer confidence, leading to brand loyalty.
Tips for achieving optimal results with casing machines include regular maintenance to ensure smooth operation and avoiding downtime. Operators should also receive thorough training to understand the functionalities and settings of the machines, allowing them to make quick adjustments when necessary. Additionally, using high-quality casings can further enhance the protective features, directly impacting the quality of the contained products.
Investing in advanced casing machine technology is essential for companies aiming to improve their production metrics. By focusing on product consistency and quality, businesses can significantly reduce waste and optimize their overall manufacturing process. Institutions that prioritize these aspects will likely see substantial returns on their investment through enhanced consumer satisfaction and increased market share.
Unlocking Efficiency with the Best Casing Machines and Their Impact on Production Metrics
Casing Machine Model | Production Speed (units/hour) | Product Quality Score (out of 100) | Consistency Rate (%) | Maintenance Frequency (per month) |
---|---|---|---|---|
Model A | 1200 | 95 | 98 | 2 |
Model B | 1500 | 90 | 95 | 3 |
Model C | 1100 | 92 | 97 | 1 |
Model D | 1300 | 89 | 93 | 2 |
Model E | 1600 | 94 | 99 | 1 |
Case Studies: How Leading Chinese Factories are Using Casing Machines Effectively
The utilization of advanced casing machines in Chinese factories is redefining production efficiency, showcasing remarkable case studies of operational excellence. By implementing these machines, leading manufacturers have significantly streamlined their processes, enhancing throughput and optimizing resource allocation. The impressive capacity of casing machines to minimize manual labor and reduce error rates is a testament to the role of automation in modern manufacturing. As factories integrate these technologies, they are not only improving their production metrics but also positioning themselves to compete in an increasingly globalized market, particularly in sectors such as electric vehicles and consumer electronics.
In the face of rapid innovation, Chinese manufacturers are not only adopting cutting-edge casing machines but are also harnessing the power of intelligent manufacturing technologies. This includes AI-driven quality inspections that ensure product reliability while maintaining high production speeds. The evolution of these practices aligns with China's broader ambition to lead in advanced manufacturing and technology innovation. As factories embrace these sophisticated tools, they are setting new benchmarks for efficiency and quality, further solidifying China's role as a powerhouse in the global supply chain landscape.